Point out the advantages and disadvantages of using 3D CMM scanners
How to ensure the size and shape of the product always meet the standard? This is a common problem in production, especially in industries that require high precision. That is also the reason why coordinate measuring machines (CMM) are increasingly appearing in the measurement laboratories of factories.
Contents
CMM helps analyze the size and geometry of the part accurately, thereby controlling product quality right from the production stage. However, is CMM the optimal choice in all cases? Let's learn about the operating principles, benefits, and limitations of CMM in the article below!
First of all, it is necessary to understand what a CMM is and what it is for?
In the manufacturing industry, how can the dimensions and shape of a part be measured accurately? A Coordinate Measuring Machine (CMM) is one of the most commonly used tools to address this challenge. CMM operates by using a probe to touch the surface of the part, recording coordinate points based on the Cartesian system. By collecting dozens or even hundreds of points, CMM can accurately reconstruct the 3D shape of the part in detail.
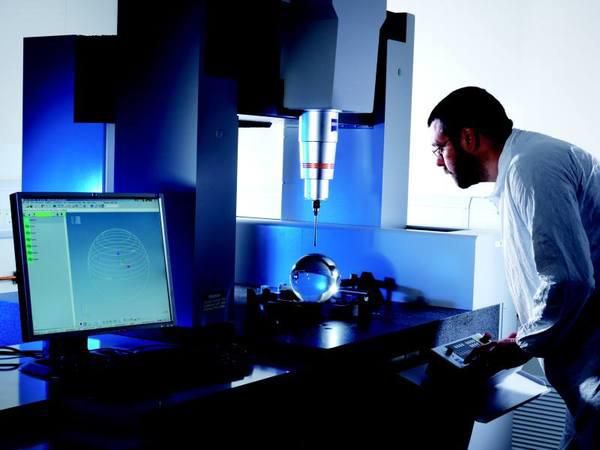
The data collected from CMM not only helps verify the part’s dimensions against technical drawings or CAD files but also supports reverse engineering and production optimization. Comparing the measured parameters with established standards ensures that the product meets the desired quality before being shipped. In industries that demand high precision, such as aerospace, automotive, and precision engineering, CMM is widely preferred for measurement tasks.
Currently, there are various types of CMMs, including bridge, gantry, horizontal arm, and articulated arm models. However, they all fundamentally consist of three main components: the base, the computer, and the probe. The base secures the part in place to prevent movement during measurement. The computer processes and analyzes the collected data. The probe directly interacts with the part’s surface to gather measurement information.
What are the benefits of CMM coordinate measuring machine?
In industrial manufacturing, controlling the dimensions and shape of a product is a key factor in ensuring quality. With its automated operation, a CMM minimizes manual intervention, reduces errors, and optimizes the inspection process.
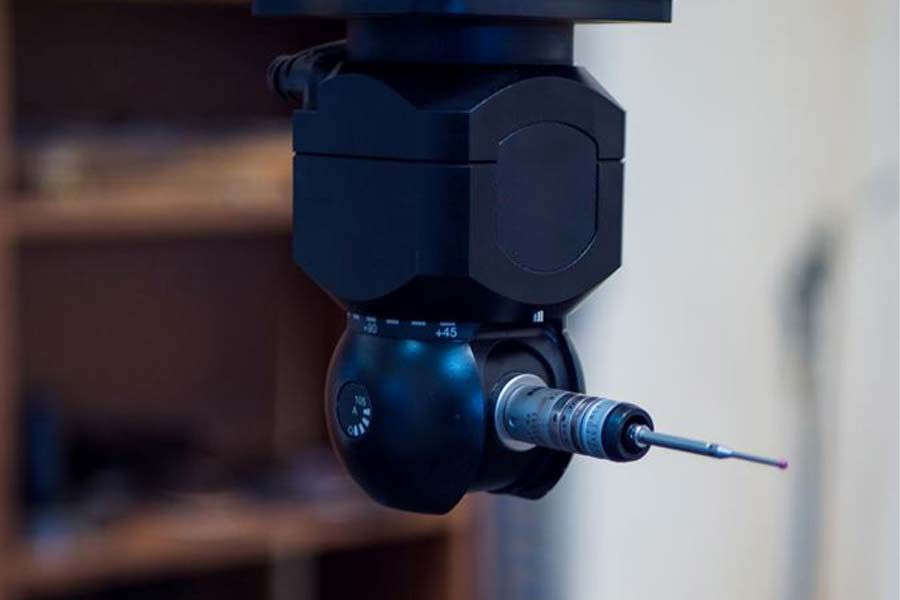
One major advantage of CMMs is their ability to be programmed to perform measurements as required. The machine can scan surfaces, collect data from multiple points, and analyze details in three-dimensional space. This allows for the verification of critical parameters against the original design without relying on time-consuming manual measurement methods. Notably, CMMs can measure not only length, width, and height but also evaluate the shape and position of features on a part, accommodating both simple and complex inspection needs.
Visible limitations
Despite the many benefits, CMMs also have some points to consider. The initial investment cost is quite high, not to mention the operation and maintenance requires certain technical expertise. Therefore, before choosing to use CMMs, businesses need to assess their actual needs to ensure cost optimization and efficiency in the production process.
Conclude:
Hopefully the above information will help you have a clearer view of the advantages and disadvantages of CMM measuring machines. If you are looking for a suitable measurement solution and need detailed advice, do not hesitate to contact EMIN for dedicated support!